VOCs
VOCs waste gas treatment
VOCs is the abbreviation for volatile organic compounds. VOCs in the ordinary sense refer to volatile organic compounds; however, the definition in the environmental sense refers to the active type of volatile organic compounds, that is, the type of volatile organic compounds that can cause harm. This article introduces in detail seven main technologies of VOC waste gas treatment.
1. VOC waste gas treatment technology
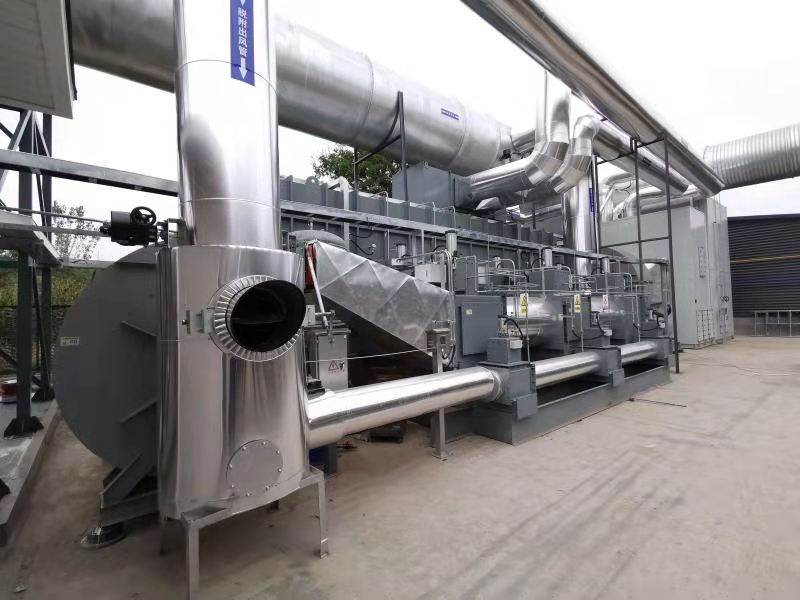
Thermal destruction method Thermal destruction method refers to the direct and auxiliary combustion of organic gas, that is, VOC, or the use of appropriate catalysts to accelerate the chemical reaction of VOC, and ultimately to reduce the concentration of organic matter, so that it is no longer harmful to a treatment method. Thermal destruction method has a better effect on the treatment of low concentration of organic waste gas, so it has been widely used in the treatment of low concentration of waste gas. This method is mainly divided into two types, namely direct flame combustion and catalytic combustion. The heat treatment efficiency of direct flame combustion on organic waste gas is relatively high, which can reach 99% in general. Catalytic combustion refers to accelerating the chemical reaction rate of organic waste gas under the action of catalytic bed. This method takes less time than direct combustion and is the preferred technology for high concentration and small flow of organic waste gas purification.
2. VOC waste gas treatment technology
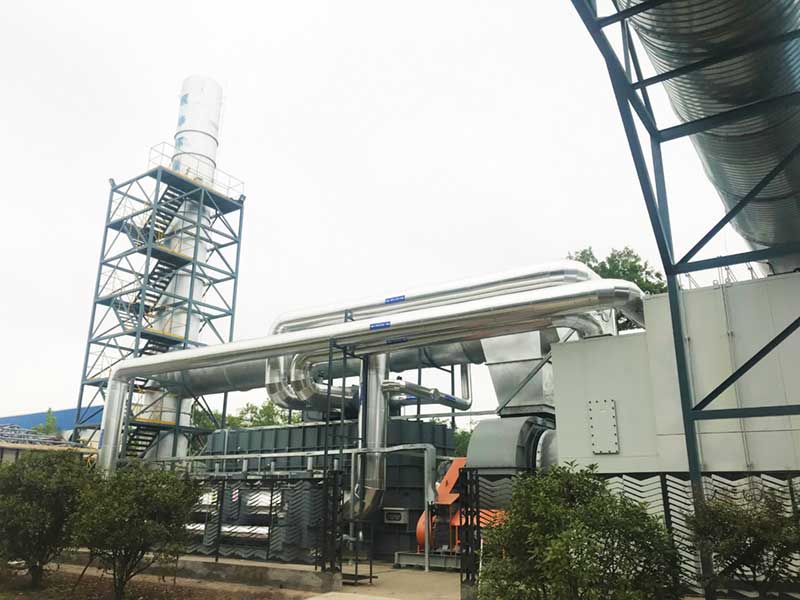
Adsorption method of organic waste gas adsorption method is mainly suitable for low concentration, high flux organic waste gas. At present, this organic waste gas treatment method has been quite mature, the energy consumption is relatively small, but the treatment efficiency is very high, and can completely purify the harmful organic waste gas. The practice proves that this method is worthy of popularization and application. But this method also has some defects, it requires a large volume of equipment, and the process is more complex; If there is a large amount of impurities in the exhaust gas, it is easy to cause poisoning of workers. Therefore, the key of using this method to treat waste gas lies in the adsorbent. At present, the adsorption method is used to treat organic waste gas, and more activated carbon is used, mainly because the fine pore structure of activated carbon is better and the adsorption is stronger. In addition, after iron oxide or ozone treatment, the adsorption performance of activated carbon will be better, and the treatment of organic waste gas will be more safe and effective.
3. VOC waste gas treatment technology
Biological treatment method from the basic principle of treatment, the use of biological treatment of organic waste gas, is the use of microbial physiological process to transform the harmful substances in the organic waste gas into simple inorganic, such as CO2, H2O and other simple inorganic. This is a harmless organic waste gas treatment. In general, a complete process of biological treatment of organic waste gas includes three basic steps: a) The organic pollutants in the organic waste gas first come into contact with water, where they can be dissolved quickly; B) Organic matter dissolved in the liquid membrane can be gradually diffused into the biofilm at a low liquid concentration, and then absorbed by microorganisms attached to the biofilm; C) The organic waste gas absorbed by microorganisms will be degraded in the process of their own physiological metabolism and eventually transformed into compounds that are not harmful to the environment.
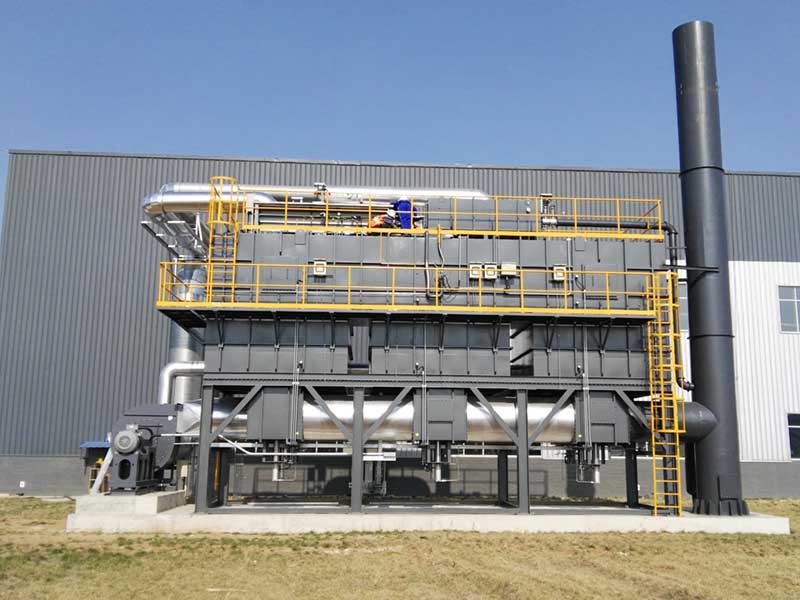
4.VOC waste gas treatment technology
Psa separation and purification technology
Pressure swing adsorption separation and purification technology is to use the characteristics of gas components can be adsorbed on solid materials, in the organic waste gas and separation and purification device, the gas pressure will change to a certain degree, through this pressure change to treat the organic waste gas.
PSA technology is mainly used in the physical method, through the physical method to achieve the purification of organic waste gas, the use of material is mainly zeolite molecular sieve. Zeolite molecular sieve has certain advantages in adsorption selectivity and adsorption capacity. At a certain temperature and pressure, the zeolite molecular sieve can adsorb organic components in the organic waste gas, and then transfer the remaining gas to the next step. After the adsorption of organic waste gas, it is transformed through a certain process to maintain and improve the regeneration capacity of the adsorbent, so that the adsorbent can be put into use again, and then repeat the previous step process, cycle repeatedly, until the organic waste gas is purified.
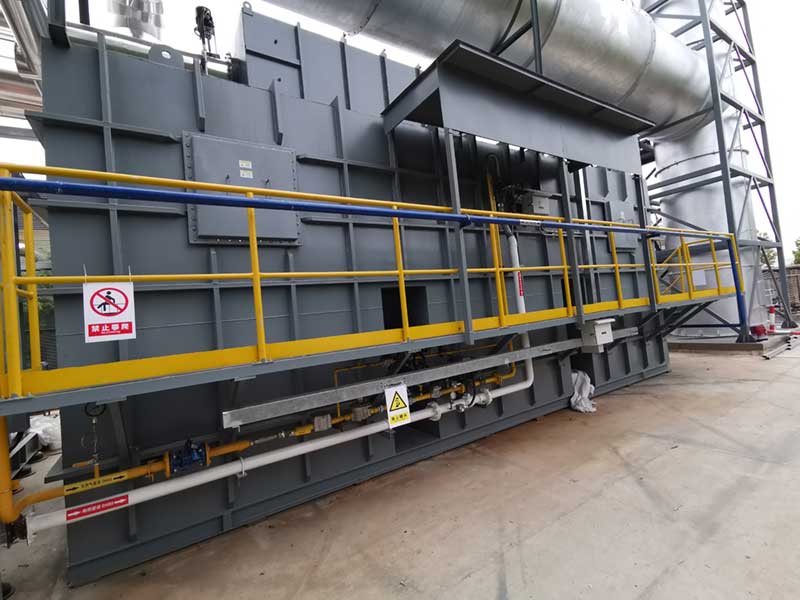
In recent years, the technology began to be applied in industrial production, and has a good effect on gas separation. The main advantages of this technology are: less energy consumption, lower cost, automation of process operation, higher purity of mixture after separation and purification, and less environmental pollution. The use of this technology has a good effect on the recovery and treatment of a certain value of gas, the market development prospect is broad, and become the future development direction of organic waste gas treatment technology.
5. VOC waste gas treatment technology
Oxidation method for toxic, harmful, and do not need to recover VOC, thermal oxidation method is the most suitable treatment technology and method. The basic principle of oxidation method: VOC reacts with O2 to generate CO2 and H2O. The chemical equation is as follows:

From the chemical reaction equation, the oxidation reaction and chemical combustion process is similar, but due to the relatively low VOC concentration, in the chemical reaction will not produce visible flame. In general, the oxidation process can ensure the smooth progress of the oxidation reaction through two methods:
A) heating. Make the organic waste gas containing VOC reach the reaction temperature;
B) Use a catalyst. If the temperature is low, the oxidation reaction can be carried out on the surface of the catalyst . Therefore, the oxidation method of organic waste gas treatment is divided into the following two methods:
a) catalytic oxidation method. At present, there are two kinds of catalysts used in catalytic oxidation, namely noble metal catalysts and non-noble metal catalysts. Noble metal catalysts mainly include Pt, Pd, etc., they are attached to the catalyst carrier in the form of fine particles, and the catalyst carrier is usually metal or ceramic honeycomb, or bulk packing; Non-noble metal catalysts are mainly made by mixing transition element metal oxides, such as MnO2, in proportion to a binder. In order to effectively prevent the catalyst from losing its catalytic activity after poisoning, the toxic substances such as Pb, Zn and Hg must be completely removed before treatment. If the catalyst poison in the organic waste gas and the covering substance can not be removed, the catalytic oxidation method can not be used to deal with VOC;
b) Thermal oxidation. Thermal oxidation method is currently divided into three types: thermal combustion type, wall type, heat storage type. The main difference between the three methods is the way heat is recovered. These three methods can be combined with catalytic methods to reduce the reaction temperature of the chemical reaction. Thermal combustion type thermal oxidizer, generally refers to the gas incinerator.
A) heating. Make the organic waste gas containing VOC reach the reaction temperature;
B) Use a catalyst. If the temperature is low, the oxidation reaction can be carried out on the surface of the catalyst . Therefore, the oxidation method of organic waste gas treatment is divided into the following two methods:
a) catalytic oxidation method. At present, there are two kinds of catalysts used in catalytic oxidation, namely noble metal catalysts and non-noble metal catalysts. Noble metal catalysts mainly include Pt, Pd, etc., they are attached to the catalyst carrier in the form of fine particles, and the catalyst carrier is usually metal or ceramic honeycomb, or bulk packing; Non-noble metal catalysts are mainly made by mixing transition element metal oxides, such as MnO2, in proportion to a binder. In order to effectively prevent the catalyst from losing its catalytic activity after poisoning, the toxic substances such as Pb, Zn and Hg must be completely removed before treatment. If the catalyst poison in the organic waste gas and the covering substance can not be removed, the catalytic oxidation method can not be used to deal with VOC;
b) Thermal oxidation. Thermal oxidation method is currently divided into three types: thermal combustion type, wall type, heat storage type. The main difference between the three methods is the way heat is recovered. These three methods can be combined with catalytic methods to reduce the reaction temperature of the chemical reaction. Thermal combustion type thermal oxidizer, generally refers to the gas incinerator.
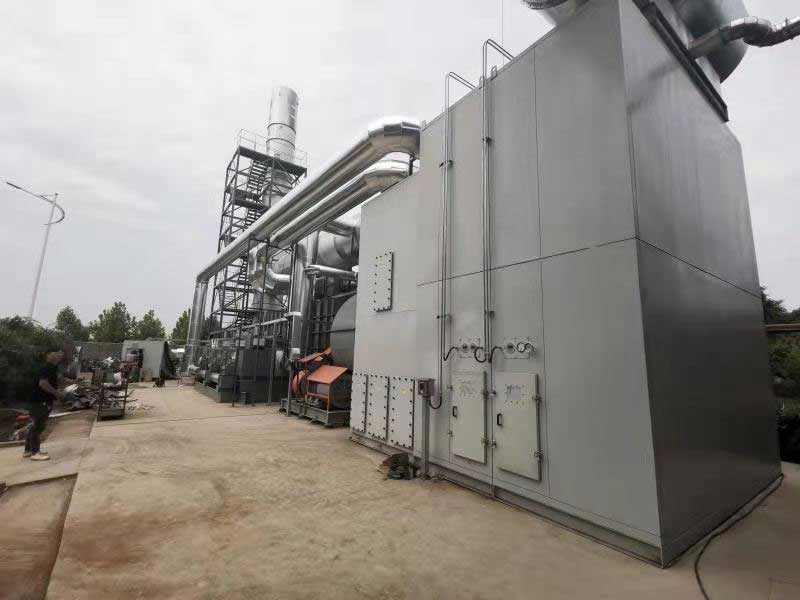
The gas incinerator consists of an accelerant, a mixing zone and a combustion chamber. Among them, accelerants, such as natural gas, oil, etc., are auxiliary fuels. In the combustion process, the heat mixing zone generated in the incinerator can preheat THE VOC waste gas. After preheating, it can provide enough space and time for the treatment of organic waste gas, and finally realize the harmless treatment of organic waste gas.
Under the condition of sufficient oxygen supply, the reaction degree of oxidation reaction -- VOC removal rate -- mainly depends on the "three T conditions" : Temperat, Time and Turbulence. The "three T conditions" are related to each other. Within a certain range, the improvement of one condition can reduce the other two conditions. The disadvantage of thermal combustion thermal oxidizer is that the high auxiliary fuel price leads to high operating cost of the device.
The inter-wall thermal oxidizer refers to the addition of the inter-wall heat exchanger in the thermal oxidation device, and then the heat of the exhaust gas from the combustion chamber is transferred to the gas at the entrance of the oxidation device at a lower temperature, and the oxidation reaction can be promoted after the preheating is completed.
At this stage, interwall heat exchangers can achieve heat recovery of up to 85%, thus significantly reducing auxiliary fuel consumption. In general, there are three types of interwall heat exchangers: tube type, shell type and plate type.
Because the temperature of thermal oxidation must be controlled in the range of 800 ℃ ~ 1 000 ℃, the heat exchange between walls must be made of stainless steel or alloy materials. So the cost of the wall heat exchanger is quite high, and this is also its disadvantages. In addition, the thermal stress of the material is also difficult to eliminate, which is another disadvantage of heat exchange between walls. Regenerative thermal oxidizer, referred to as RTO, is included in the regenerative heat exchanger in the thermal oxidation device, and oxidation reaction can be carried out after the completion of VOC preheating.
At present, the heat recovery rate of regenerative thermal oxidizer has reached 95%, and its space is relatively small, and the consumption of auxiliary fuel is relatively small. As current heat storage materials can use ceramic fillers, they can handle corrosive or particulate VOC gases.
At present, RTO devices are divided into two types: rotary type and valve switching type. Among them, the valve switching type is the most common type, consisting of two or more ceramic packed beds, which can change the direction of air flow by switching the valve.
Under the condition of sufficient oxygen supply, the reaction degree of oxidation reaction -- VOC removal rate -- mainly depends on the "three T conditions" : Temperat, Time and Turbulence. The "three T conditions" are related to each other. Within a certain range, the improvement of one condition can reduce the other two conditions. The disadvantage of thermal combustion thermal oxidizer is that the high auxiliary fuel price leads to high operating cost of the device.
The inter-wall thermal oxidizer refers to the addition of the inter-wall heat exchanger in the thermal oxidation device, and then the heat of the exhaust gas from the combustion chamber is transferred to the gas at the entrance of the oxidation device at a lower temperature, and the oxidation reaction can be promoted after the preheating is completed.
At this stage, interwall heat exchangers can achieve heat recovery of up to 85%, thus significantly reducing auxiliary fuel consumption. In general, there are three types of interwall heat exchangers: tube type, shell type and plate type.
Because the temperature of thermal oxidation must be controlled in the range of 800 ℃ ~ 1 000 ℃, the heat exchange between walls must be made of stainless steel or alloy materials. So the cost of the wall heat exchanger is quite high, and this is also its disadvantages. In addition, the thermal stress of the material is also difficult to eliminate, which is another disadvantage of heat exchange between walls. Regenerative thermal oxidizer, referred to as RTO, is included in the regenerative heat exchanger in the thermal oxidation device, and oxidation reaction can be carried out after the completion of VOC preheating.
At present, the heat recovery rate of regenerative thermal oxidizer has reached 95%, and its space is relatively small, and the consumption of auxiliary fuel is relatively small. As current heat storage materials can use ceramic fillers, they can handle corrosive or particulate VOC gases.
At present, RTO devices are divided into two types: rotary type and valve switching type. Among them, the valve switching type is the most common type, consisting of two or more ceramic packed beds, which can change the direction of air flow by switching the valve.
6. VOC waste gas treatment technology -- liquid absorption method
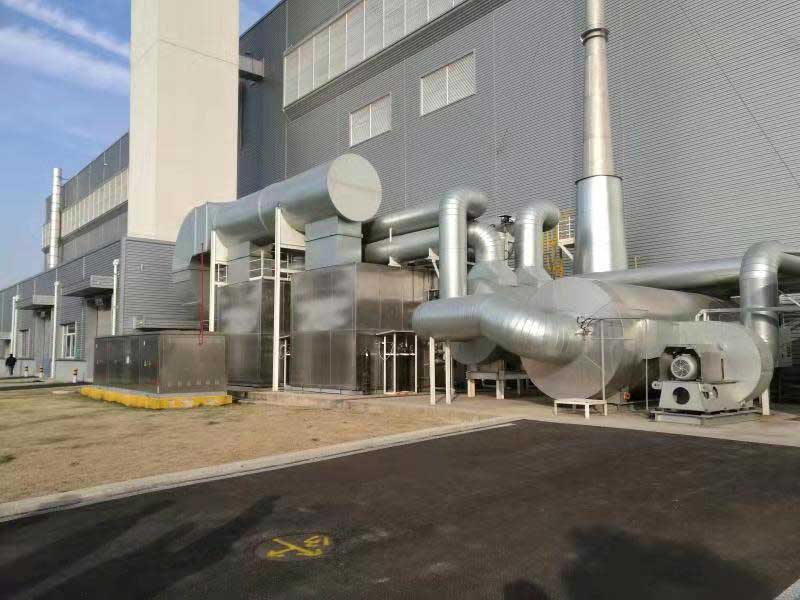
Liquid absorption method refers to the transfer of harmful molecules in the organic waste gas to the absorbent through the contact between the absorbent and the organic waste gas, so as to achieve the purpose of separating the organic waste gas. This treatment method is a typical physical and chemical process. After the organic waste gas is transferred to the absorbent, the harmful molecules in the absorbent are removed by analytical method, and then recycled to realize the reuse and utilization of the absorbent.
From the perspective of the principle of action, this method can be divided into chemical method and physical method. Physical method refers to the use of the principle of phase dissolution between substances, water as an absorber, to remove harmful molecules in organic waste gas, but for insoluble waste gas, such as benzene, can only be removed by chemical methods, that is, through the chemical reaction between organic waste gas and solvent, and then to be removed.
7. VOC waste gas treatment technology - condensation recovery method
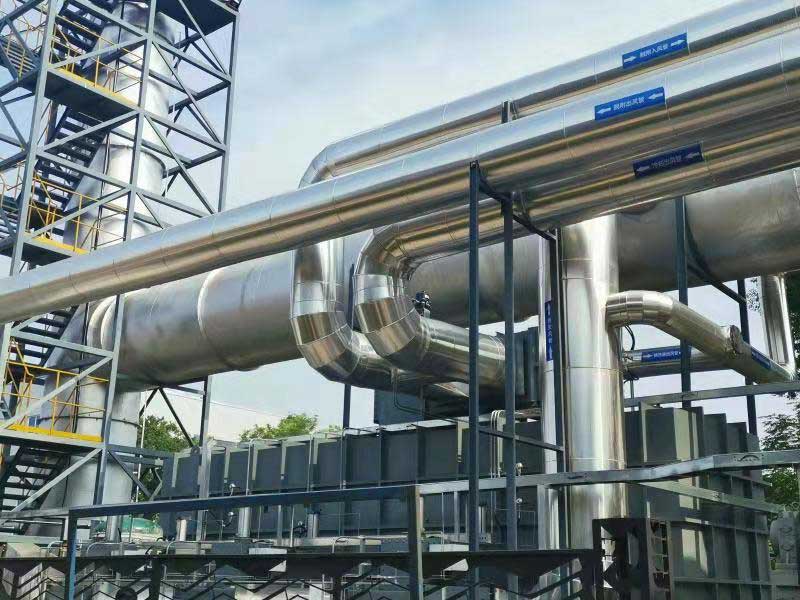
At different temperatures, the saturation of organic matter is different, the condensation recovery method is to use the characteristics of organic matter to play a role, by reducing or increasing the system pressure, the organic matter in the steam environment through condensation extraction. After condensation extraction, the organic waste gas can be highly purified. Its disadvantage is that it is difficult to operate, and it is not easy to complete with cooling water at room temperature. It needs to cool the condensate water, so it needs more costs. This treatment method is mainly suitable for organic waste gas treatment with high concentration and low temperature.