Sludge
Sludge treatment technology
The solid material separated or retained in the treatment of domestic sewage and industrial wastewater is called sludge. As a by-product of sewage treatment, sludge usually contains a large number of substances that are toxic, harmful or have a negative impact on the environment. It must be handled properly, or there will be secondary pollution.
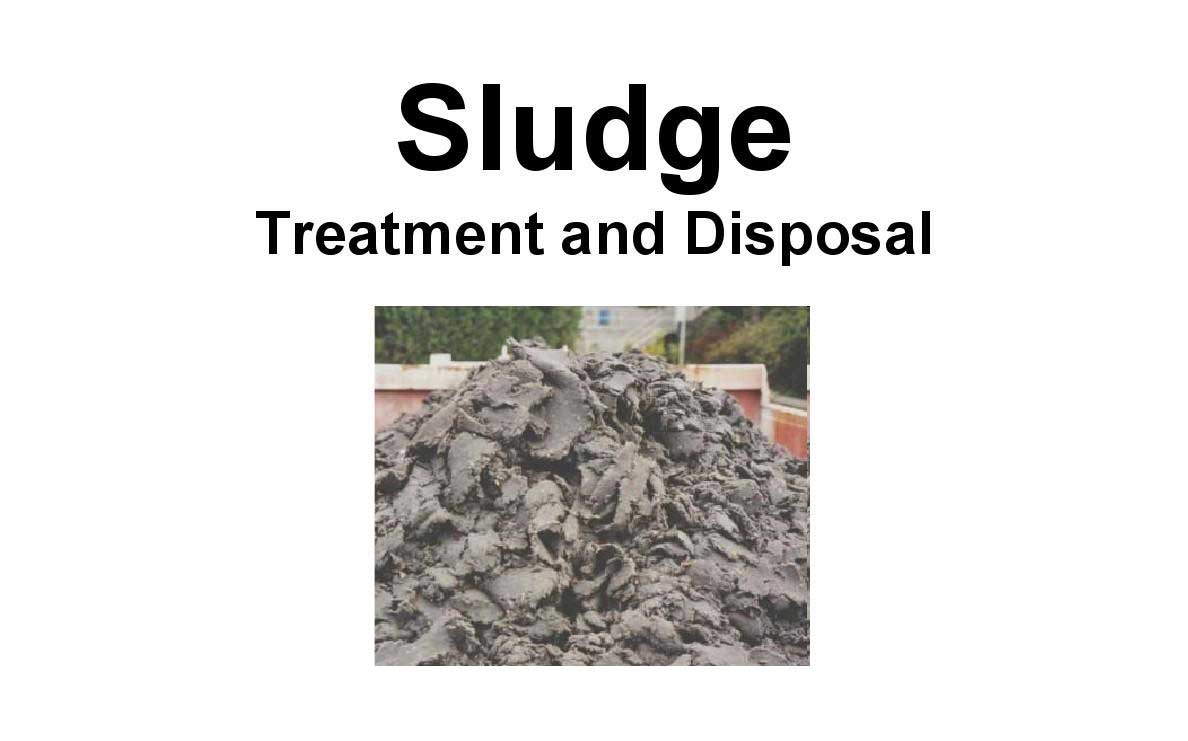
The solid substances in the sludge may already exist in the sewage, such as suspended substances trapped in various natural sedimentation tanks; It may also be formed in the process of sewage treatment, such as biological treatment and chemical treatment process, biological blood hoofs and suspended substances from the original dissolved substances and alternate substances transformation; It could also be caused by chemicals added to the sewage treatment process. When the solid material is mainly organic matter, it is called sludge; When it is mainly inorganic, it is called sludge.
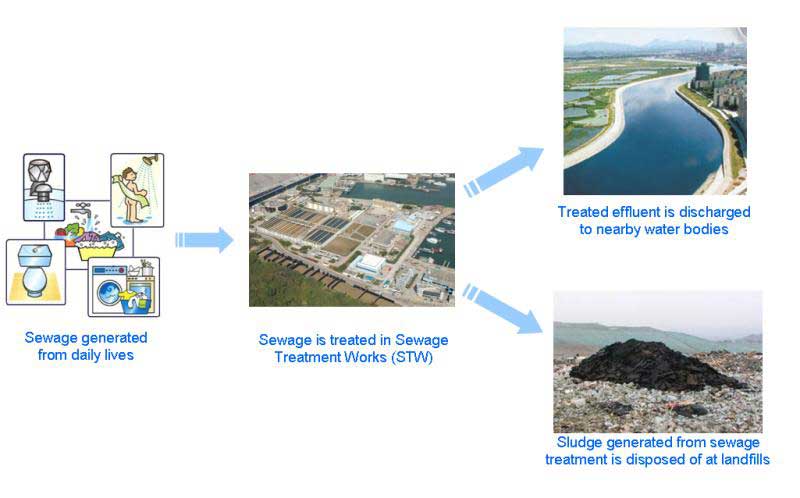
The goal of sludge treatment and disposal is to realize the reduction, stabilization, harmless and resource utilization of sludge. Sludge treatment and disposal can be divided into two stages from the technical and operational level. The first stage is to reduce and stabilize the sludge in the sewage treatment plant or in a centralized way. Its purpose is to reduce the risk of secondary pollution caused by the outward transport of sludge after treatment. The second stage is the reasonable and safe disposal of the sludge after treatment, so that the sludge can achieve the purpose of harmless and resource, this stage is mainly the category of sludge dewatering.
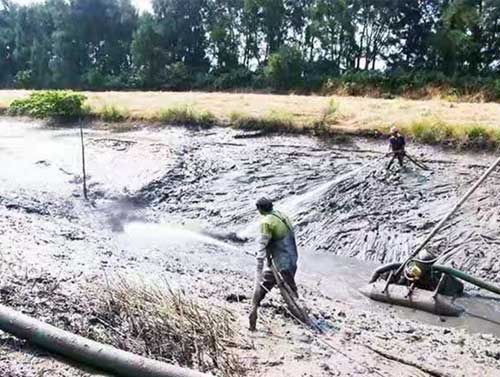
Sewage will produce a large amount of sludge after precipitation treatment, even after concentration and digestion treatment, water content is still up to 96%, large volume, it is difficult to consume disposal, must be dehydrated treatment, improve the solid content of mud cake, in order to reduce the footprint of sludge heap. Generally, mechanical dehydration is adopted in large and medium-sized sewage treatment plants. There are many kinds of dehydrators. According to the dehydration principle, it can be divided into vacuum filtration dehydration, pressure filtration dehydration, stacked screw dehydration and centrifugal dehydration.
The solid material separated or retained in the treatment of domestic sewage and industrial wastewater is called sludge. As a by-product of sewage treatment, sludge usually contains a large number of substances that are toxic, harmful or have a negative impact on the environment. It must be handled properly, or there will be secondary pollution. The solid substances in the sludge may already exist in the sewage, such as suspended substances trapped in various natural sedimentation tanks; It may also be formed in the process of sewage treatment, such as biological treatment and chemical treatment process, biological blood hoofs and suspended substances from the original dissolved substances and alternate substances transformation; It could also be caused by chemicals added to the sewage treatment process. When the solid material is mainly organic matter, it is called sludge; When it is mainly inorganic, it is called sludge. The goal of sludge treatment and disposal is to realize the reduction, stabilization, harmless and resource utilization of sludge. Sludge treatment and disposal can be divided into two stages from the technical and operational level. The first stage is to reduce and stabilize the sludge in the sewage treatment plant or in a centralized way. Its purpose is to reduce the risk of secondary pollution caused by the outward transport of sludge after treatment. The second stage is the reasonable and safe disposal of the sludge after treatment, so that the sludge can achieve the purpose of harmless and resource, this stage is mainly the category of sludge dewatering.
Sewage will produce a large amount of sludge after precipitation treatment, even after concentration and digestion treatment, water content is still up to 96%, large volume, it is difficult to consume disposal, must be dehydrated treatment, improve the solid content of mud cake, in order to reduce the footprint of sludge heap. Generally, mechanical dehydration is adopted in large and medium-sized sewage treatment plants. There are many kinds of dehydrators. According to the dehydration principle, it can be divided into vacuum filtration dehydration, pressure filtration dehydration, stacked screw dehydration and centrifugal dehydration.
1. The belt filter dewatering machine
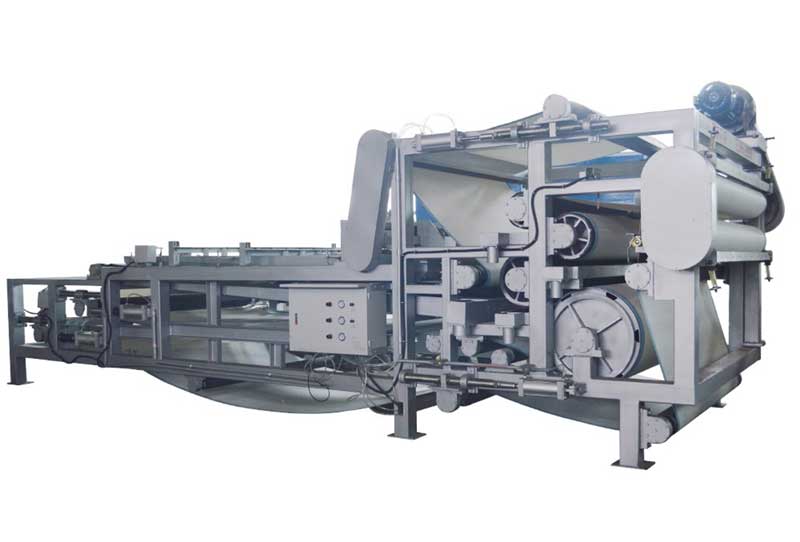
belt type filter dewatering machine is made up of up and down two tension belt with sludge layer, from a series of regularly arranged roller pressure in the cylinder is S form, rely on the tension of belt itself form a crushing and shearing force of the sludge layer, the layer of sludge water capillary extrusion, obtain higher solid content of mud cake, so as to realize sludge dewatering. The general belt press filter dehydrator is composed of the filter belt, the roller cylinder, the filter belt tensing system, the filter belt adjusting system, the filter belt flushing system and the filter belt driving system. When selecting the model, the following aspects should be considered: (L) filter belt. It is required to have high tensile strength, resistance to twists and turns, acid and alkali resistance, resistance to temperature changes and other characteristics, at the same time should also consider the specific properties of the sludge, select suitable braid texture, so that the filter belt has good air permeability and sludge particles interception performance (2) roll cylinder deviation system. It is usually done by pneumatic device. (3) the tension system of the filter belt. It is also controlled by pneumatic system. The tension of the filter belt is generally controlled in 0.3-0.7mpa, and the commonly used value is 0.5mpa. (4) speed control. Different properties of sludge have different requirements for strip speed, that is, there is an optimal strip speed control range for any particular sludge, in which the dewatering system can not only guarantee certain processing capacity, but also get high quality mud cake. The belt filter press has several disadvantages: (1) the belt filter press has a large water consumption for washing the filter belt, and the washing is not complete, which is easy to cause the filter belt to be blocked; (2) The belt of the belt filter press is easy to run off, and the filter material is easy to run, the filter material contains gravel, and the equipment is easy to wear; (3) The field environment of the belt filter press is poor, the odor is relatively large, and the seepage control treatment is improper, which may pollute the groundwater; (4) Belt filter press is not suitable for small density or liquid density is greater than the solid phase material dehydration, the particle size should be greater than 0.01 mm;
⑤ The filter effect of the belt filter press is unstable, which is greatly affected by natural factors such as season, temperature and light.
2. Centrifugal dewatering machine
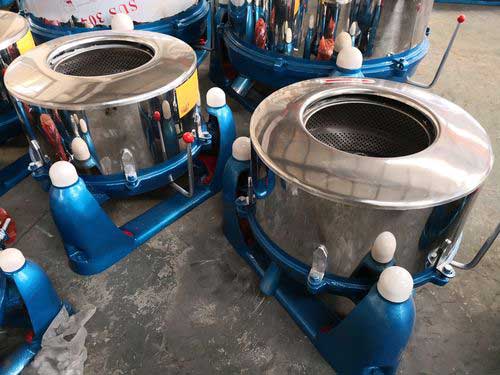
centrifugal dewatering machine is mainly composed of transfer and a spiral conveyor with a hollow shaft. The sludge is sent into the rotary cylinder by the hollow shaft, and under the action of centrifugal force generated by high-speed rotation, it is immediately thrown into the rotary hub cavity. The proportion of sludge particles is larger, so the centrifugal force is larger, which is thrown on the inner wall of the hub, forming a solid layer; Water density is small, centrifugal force is small, only in the solid layer inside the liquid layer. The solid layer of sludge is slowly pushed by the spiral conveyor to be transported to the cone end of the transfer, and continuously discharged through the outlet around the transfer, while the liquid is discharged from the overflow of weir four to the transfer, and then collected back out of the dehydrator. The most critical part of centrifugal dehydrator is the hub, the larger the diameter of the hub, the greater the dehydration capacity, but the manufacturing and operation costs are quite high, very uneconomic. The longer the length of the transfer, the higher the solid content of sludge, but the transfer too long will make the performance price reduction. In the process of use, the speed of transfer is an important control parameter, to control the speed of the hub, so that it can not only obtain higher solid content but also reduce energy consumption, is the key to the operation of centrifugal dehydrator. At present, low speed centrifugal dehydrators are mostly used. In the selection of centrifugal dehydrator, because the outer edge of the runner or spiral is easy to wear, there are special requirements for its material.
3. Plate and frame press filter dehydrator
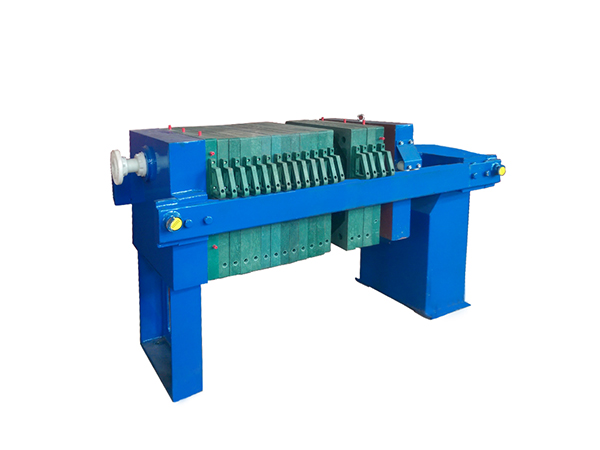
Plate and frame press filter dehydrator plate and frame press is through the plate and frame extrusion, so that the water in the sludge discharged through the press cloth, to achieve the purpose of dehydration. It is mainly composed of concave filter plate, frame, automatic and pneumatic closure system test plate suspension system, filter plate vibration system, air compression device, press cloth high pressure washing device and photoelectric protection device on one side of the fuselage, etc. When selecting the equipment, the following aspects should be considered: (1) the requirements for the solid content of mud cake. Compared with other types of dehydrators, the general plate and frame filter press has the highest solid content of mud cake, which can reach 35%. If considering the factors of reducing sludge heap and occupation, the plate and frame filter press should be the first choice. (2) The material of the frame. (3) Material of filter plate and filter cloth. It is required to be corrosion resistant and the press cloth should have a certain tensile strength. (4) The movement mode of the filter plate. Requirements can be completed by a hydraulic pneumatic device automatic or semi-automatic, in order to reduce the labor intensity of the operator. (5) Press cloth oscillating device to make the filter cake easy to fall off. Compared with other types of dehydrators, the biggest disadvantage of plate and frame filter press is that it occupies a large area. Because of the discontinuous operation of the plate and frame filter press, the efficiency is low, the operating room environment is poor, and there are secondary pollution, the domestic large sewage plant has rarely used. But nearly a great deal of development work, make it adapt to the requirement of modern wastewater treatment plant, such as system control can be achieved by PLC system all the way, the filter, the filter plate movement, the oscillation of the filter cloth, compressed air, washing of filter cloth, the operations such as the feed all can be done through PLC remote control, reduce the labor intensity of workers.
4. Stacked screw dehydrator
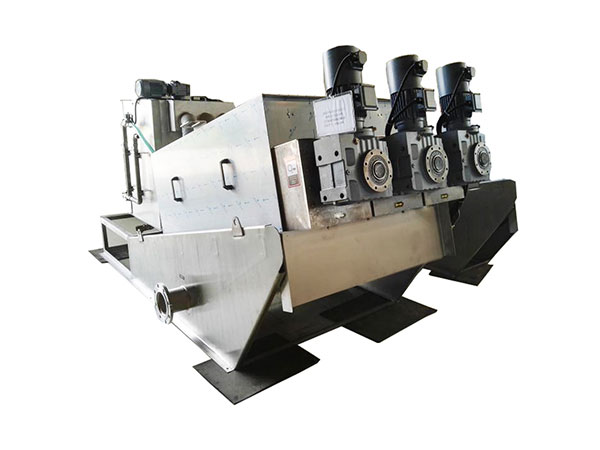
Stacked screw dehydrator
(1) The development of early filter: Early filter first appeared in Germany, and then in the former Soviet union, Sweden, the United States and other countries also have to make this kind of filter, and the earliest application in oil and fish meat after grinding squeeze dewatering, fish, shrimp waste filter, in recent years, especially in sludge dewatering, and other industrial processes, and other fields has been widely used. German mechanical engineer invented a relatively new filter structure, the moving and fixed ring filter structure. The fixed ring and the movable ring are separated from each other, and there is a certain filter gap. Through the friction between the movable ring and the fixed ring, the friction force that promotes the extrusion of the material is greater than the obstruction effect, so as to improve the filtration and separation effect of the material, and avoid the blockage phenomenon of high viscosity material.
(2) Development of the folding screw machine in Japan: Japan designed and modified the machine shape and registered it as the folding screw trademark, and the owner of the trademark is Anikan. The official name of the machine was formed at this time.
(3) Development of the screw folding machine in China and other regions: subsequent screw folding machine technology was introduced to many other countries, including China. In recent years, the folding machine in China's chemical, printing and dyeing, municipal, textile, medicine, food and other industries play a huge role. The working principle is divided into the following aspects :1. Concentration. When the screw pushes the axis to rotate, the multiple solid and movable laminated sheets located on the periphery of the pushing axis move relatively, and under the action of gravity, the water filters out from the relatively moving laminated gap to achieve rapid concentration. 2. Dewatering, the concentrated sludge moves forward with the rotation of the spiral axis; Along the outlet direction of the mud cake, the pitch of the spiral axis gradually decreases, the gap between the rings also gradually decreases, and the volume of the spiral cavity shrinks constantly. Under the action of the back pressure plate at the outlet, the internal pressure is gradually increased, and the water in the sludge is extruded and discharged under the continuous operation of the spiral driving shaft, and the solid content of the filter cake is constantly rising, and the continuous dehydration of sludge is finally realized. 3. Self-cleaning, the rotation of the spiral shaft drives the moving ring to rotate constantly. The equipment relies on the movement between the fixed ring and the moving ring to realize the continuous self-cleaning process, so as to skillfully avoid the blockage problem commonly existed in the traditional dehydrator.
(1) The development of early filter: Early filter first appeared in Germany, and then in the former Soviet union, Sweden, the United States and other countries also have to make this kind of filter, and the earliest application in oil and fish meat after grinding squeeze dewatering, fish, shrimp waste filter, in recent years, especially in sludge dewatering, and other industrial processes, and other fields has been widely used. German mechanical engineer invented a relatively new filter structure, the moving and fixed ring filter structure. The fixed ring and the movable ring are separated from each other, and there is a certain filter gap. Through the friction between the movable ring and the fixed ring, the friction force that promotes the extrusion of the material is greater than the obstruction effect, so as to improve the filtration and separation effect of the material, and avoid the blockage phenomenon of high viscosity material.
(2) Development of the folding screw machine in Japan: Japan designed and modified the machine shape and registered it as the folding screw trademark, and the owner of the trademark is Anikan. The official name of the machine was formed at this time.
(3) Development of the screw folding machine in China and other regions: subsequent screw folding machine technology was introduced to many other countries, including China. In recent years, the folding machine in China's chemical, printing and dyeing, municipal, textile, medicine, food and other industries play a huge role. The working principle is divided into the following aspects :1. Concentration. When the screw pushes the axis to rotate, the multiple solid and movable laminated sheets located on the periphery of the pushing axis move relatively, and under the action of gravity, the water filters out from the relatively moving laminated gap to achieve rapid concentration. 2. Dewatering, the concentrated sludge moves forward with the rotation of the spiral axis; Along the outlet direction of the mud cake, the pitch of the spiral axis gradually decreases, the gap between the rings also gradually decreases, and the volume of the spiral cavity shrinks constantly. Under the action of the back pressure plate at the outlet, the internal pressure is gradually increased, and the water in the sludge is extruded and discharged under the continuous operation of the spiral driving shaft, and the solid content of the filter cake is constantly rising, and the continuous dehydration of sludge is finally realized. 3. Self-cleaning, the rotation of the spiral shaft drives the moving ring to rotate constantly. The equipment relies on the movement between the fixed ring and the moving ring to realize the continuous self-cleaning process, so as to skillfully avoid the blockage problem commonly existed in the traditional dehydrator.